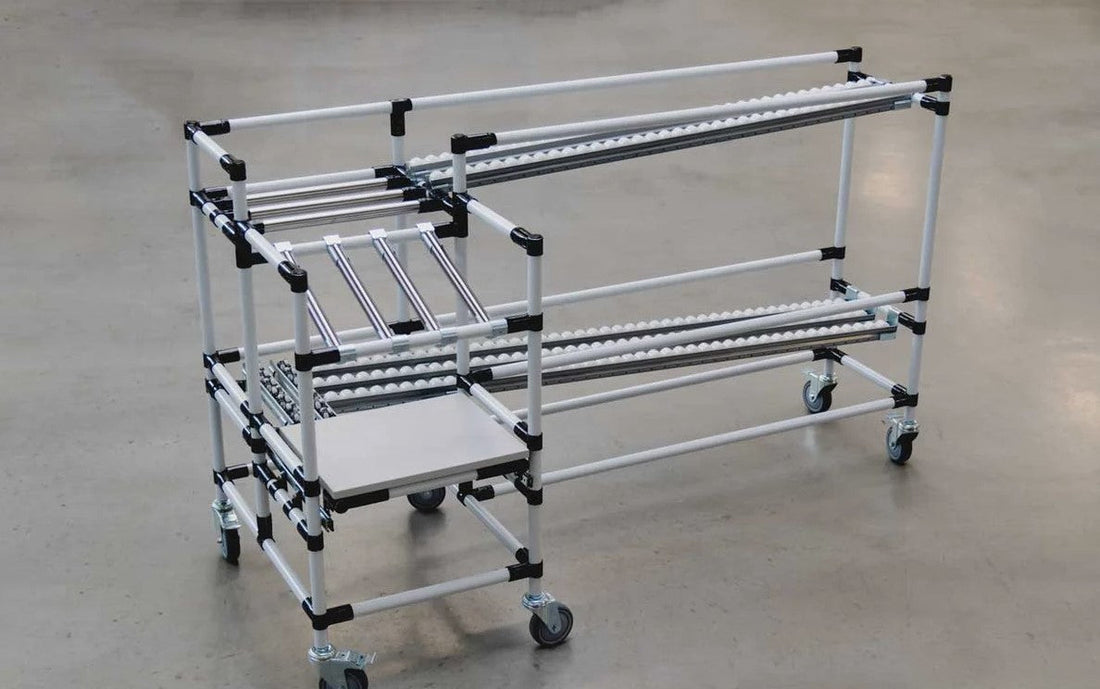
What is Lean?
Share
What is Lean?
Lean Production is a philosophy and set of methods that aims to create more value for the customer by identifying and eliminating waste. Originally developed by Toyota through the Toyota Production System (TPS), Lean is based on five core principles:
- Value – Understand what the customer truly values and eliminate elements that do not add value.
- Value Stream Mapping – Map all steps in the process and identify inefficiencies using Value Stream Mapping.
- Flow – Optimize processes to minimize wait times and create a smooth workflow.
- Pull system – Produce only what is demanded, reducing overproduction and unnecessary inventory.
- The pursuit of perfection – Lean is a continuous improvement journey where each step aims to further optimize the business.
By implementing these principles, you can create more efficient and sustainable production.
Build your own Lean Shop with us
Building a Lean Shop means creating a work environment where everything is optimized to support efficient and flexible production processes. At Virtual Manufacturing, we offer a complete solution where we help you to:
- Plan and design your Lean Shop – We analyze your business and develop a solution tailored to your needs.
- Choosing the right components – We offer modular and flexible solutions for flow racks, workstations, kit carts and shuttle solutions.
- Provide drawings and construction – Do you need support in building your own solutions? We create drawings so you can assemble yourself.
- Train your team – We ensure that your team has the right knowledge to work according to Lean principles.
Eliminate the 7 wastes with Lean
One of the most important aspects of Lean is identifying and eliminating waste. The seven types of waste in production are:
- Overproduction – Producing more than is needed.
- The wait – Unnecessary downtime in the process.
- Transportation – Unnecessary movement of materials and products.
- Overprocessing – Unnecessary production steps that do not add value.
- Warehouses – Too large warehouses tie up capital and space.
- Movement – Inefficient work movements of operators.
- Defects – Poor quality that leads to rework and scrapping.
By implementing a Lean Shop, you can minimize these wastes and create a smoother and more cost-effective operation.
Training and implementation support
To succeed with Lean, it is important that the entire team understands the philosophy and methods. We offer training and workshops where we go through:
- The basics of Lean and the five principles
- How to identify and eliminate waste
- How to build and implement a Lean Shop
- Practical exercises with Mini Karakuri and modular systems
Do you want to take the next step and build your own Lean Shop? Contact us today and we'll help you get started!